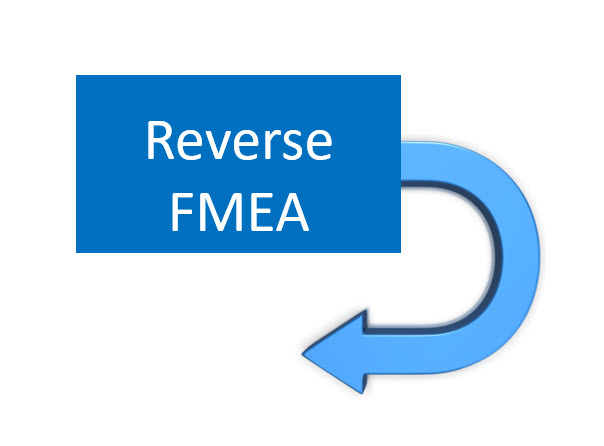
Top 10 Things You Need to Know About Reverse FMEAs
This story was originally published by Quality Digest on July 5 2022.
On Dec. 7, 2021, Ford Motor Co. updated its IATF 16949—“Customer specific requirements” (CSR), which require the use of reverse FMEAs (RFMEA) on new equipment (“tooling”). The first sentence of the reverse FMEA requirement reads: “Organizations are required to have a process in place that ensures all new launches complete an RFMEA event once the equipment is installed and running.”
As one might expect, multiple webinars are offered by RFMEA training providers, as well as two-day RFMEA classes ranging in price from $795 to $995. My guess is that it won’t be long before RFMEA software is available for purchase.
Having spent six years as a Ford plant and equipment design engineer, and an additional 32 years afterward helping companies manage new tooling risk, I see significant problems with the RFMEA processes being proposed by RFMEA training providers. Ford’s objective in requiring companies to use the RFMEA is to ensure that their suppliers effectively manage tooling risk.
Unfortunately, the RFMEA process currently being taught by RFMEA training providers won’t deliver the level of tooling quality that implementing an effective, risk-based tooling quality management system (QMS)—which is required by the automotive industry and already implemented in many companies—will provide. When describing what a RFMEA is, Nathan Stroud, Ford Global STA Six Sigma, stated, “This is a process that many of you probably already do.” (“Ford Customer-Specific Requirements (2022 update)—Explained by Ford,” webinar, Feb. 16, 2022.)
Before you decide to invest in RFMEA training, there are 10 things you need to know:
1. There are no recognized standards for how to perform an RFMEA
2. There are no standard RFMEA form or RFMEA reports
3. There are no RFMEA experts
4. Standardized tools to manage tooling risk exist in the automotive industry that negate the need for the RFMEA when used correctly
5. There is a lack of understanding of how to properly use the available standardized tools to manage tooling risk
6. The most common mistake made when performing a PFMEA on new tooling
7. How the most common PFMEA mistake led to creating the RFMEA
8. Why the RFMEA as commonly defined by RFMEA providers is ineffective and expensive
9. The Ford RFMEA definition and how it differs from the most common RFMEA definition
10. What you should do to meet the new Ford RFMEA use requirement
1. There are no recognized standards for how to perform an RFMEA
There are no documented, accepted standards for how to perform an RFMEA. As you investigate the increasing amount of information available in webinars and literature by RFMEA training providers, the differences in opinion of what an RFMEA is clearly demonstrates the impact of not having an RFMEA standard.
2. There is no standard RFMEA form or RFMEA report
There is no standard RFMEA form to fill out or an accepted group of RFMEA reports to be filed. Despite this fact, don’t be surprised to see new software advertising an RFMEA form or group of RFMEA reports to meet the new RFMEA requirement.
3. There are no RFMEA experts
When there’s no standard for what an RFMEA is, there can be no experts on how to interpret and implement it.
4. Standardized tools to manage tooling risk exist in the automotive industry that negate the need for the RFMEA
Those already familiar with managing tooling risk know that there are five types of risk that must be managed during the tooling life cycle, which begins with defining customer requirements for the tooling and ends with tooling disposal, if special disposal is required. More specifically, these are:
1. Incorrect definition of customer requirements
2. Incorrect definition of tooling design requirements to meet the customer requirements
3. Incorrect tooling design
4. Incorrect use of tooling
5. Tooling not built to tooling design specifications
Additionally, there are four core risk management tools typically found in an effective tooling QMS:
1. Requirements risk assessment
2. Machinery FMEA
3. Process FMEA on tooling use
4. Process FMEA on building tooling
The four core tools are designed to manage specific risks and must be integrated to be effective. The tooling risk-management tools that most people have heard of are: the machinery FMEA (MFMEA), which is used during the tooling design stage; and a process FMEA (PFMEA), which covers the use of the tooling itself. A strong tooling QMS also includes a PFMEA performed on the process used to build the tooling, but this is rarely done because it’s not required by the automotive industry.
5. There is a lack of understanding of how to properly use the available standardized tools for managing tooling risk
There is a significant lack of understanding within the automotive industry and tooling industry on how to use risk-management tools like the MFMEA and PFMEA to manage tooling risk. One only needs to watch RFMEA webinars and read RFMEA literature to find proof of this. A common misconception is that the purpose of the PFMEA is to manage tooling design-related risk. The actual purpose of the PFMEA is to manage risk due to improper use of tooling that has been designed. The PFMEA assesses the adequacy of tooling hardware-use aids such as poka-yoke devices, use instructions, and maintenance instructions for using the tooling as the designer intended. The main tool for managing tooling design-related risk is the MFMEA.
6. The most common mistake made when performing a PFMEA on new tooling
The most common mistake made when performing a PFMEA on new tooling is to perform it before the tooling design is complete. There are also many instances when the PFMEA is performed before completing the design of the product that the tooling is supposed to produce. If these two conditions exist when the PFMEA is attempted, it requires assessing the risks of using tooling that hasn’t been designed for producing a product that hasn’t been designed. Those attempting the PFMEA must then guess what the installed tooling will look like, as well as how the product is being produced.
7. How the most common PFMEA mistake led to creating the RFMEA
If a PFMEA is performed on tooling when its design isn’t complete, there’s a high likelihood that the tooling design will be considerably different from the tooling that is installed in the customer’s plant. Because the PFMEA drives the content of the process control plan, this can lead to failure causes being missed or improperly defined in the PFMEA, as well as improper or missing prevention controls in the process control plan. If one adds the additional condition that the PFMEA is performed before the product design is complete, there is the high probability that the failure mode column of the PFMEA and detection controls column of the process control plan will be improperly populated.
It’s for this reason that the core RFMEA activity identified by all the RFMEA training providers that I’ve reviewed is performing a PFMEA on the tooling after it has been installed in the customer plant to validate the contents of the original PFMEA. RFMEA training providers stress the need for performing a PFMEA on the installed equipment to detect new failure modes, new failure causes, and/or problematic prevention and detection controls that weren’t detected by the previously performed PFMEA.
Following are two typical comments from RFMEA training providers about the relationship between the PFMEA performed before the tooling design and product design are complete and the RFMEA performed on the tooling after it’s installed at the customer plant.
“Reverse FMEA is an activity where you begin out on the line… at the actual point of work… and work your way backward to validate the FMEA. This is a bottom-up event that provides validation and real-world applicability to the FMEA.”
—Jeremy Hazel, Plexus, “Ford Customer-Specific requirements (2022 update)—Explained by Ford,” webinar, Feb. 16, 2022
“So the reverse FMEA utilizes the flowchart, the PFMEA, and the control plan, and assesses whether they’ve been done effectively, whether the rankings are effective, and whether there are any new risks that can be identified. PFMEAs are done early in the development process as a preventive analysis, sometimes before the machines are even ordered, and sometimes before they’re installed in the plant. Eventually there’s a production FMEA that gets completed, but usually it’s done in advance with theories on how to prevent issues and how to detect issues. But they may not have the same risk once the evaluation is done. So, the reverse FMEA is performed to look at these preventive and detective controls that were identified in the PFMEA and make sure the risks that were associated with the preventive and detective controls were correct. After the reverse FMEA, there may be an adjustment of those rankings. It’s also used to focus on each operation and maybe identify additional risks that the original PFMEA team may have missed when they were doing the original evaluation.”
—Michael Down, Omnex, “Benefits of Reverse FMEA for Managing and Mitigating Production Risk,” webinar, Nov. 9, 2021
8. Why the RFMEA as commonly defined by RFMEA training providers is ineffective and expensive
Discovering tooling-design issues after tooling is installed at the customer plant is too late. It can result in high costs due the need for tooling hardware or software redesign, excessive startup scrap and rework, and delayed startup and related product-delivery costs.
It’s important to understand that the tooling a customer purchases comprises three components: tooling hardware/software, tooling use instructions, and a tooling maintenance plan. When a properly implemented tooling QMS is in use, as required by the automotive industry, most of the potential tooling design, use, and maintenance issues will be found prior to shipping the tooling to the customer.
The key activities contained in an effective QMS to make sure the tooling provider has properly defined all three components include:
1. Performing the MFMEA and supporting tooling-design verification plan. Elements of the tooling-design verification plan are performed both before and after building the tooling at the tooling-provider plant floor. The design verification performed on the tooling-provider plant floor includes testing the function of the tooling to produce the desired product at the desired rate and quality level. It also includes testing all manufacturing aids, such as poka-yoke devices and red rabbits.
2. Performing a PFMEA on the tooling use, which is conducted at three different times. The first PFMEA is performed after the tooling design is complete and ready for release but prior to building and installing the tooling on the tooling-provider plant floor. Using the first PFMEA as a starting point, the second PFMEA is performed after the tooling is built and installed on the tooling-provider plant floor. Using the second PFMEA as the starting point, the third PFMEA is performed after the tooling is built on the customer plant floor. Tooling design engineers and tooling customer personnel responsible for the use and maintenance of the tooling participate in all three PFMEAs.
3. Process validation testing is performed on the tooling after installing it at the tooling-provider plant. The results of the process validation testing of the tooling at the tooling-provider plant are used to set the occurrence ratings for the MFMEA and the PFMEA on the tooling after the installation.
4. Process validation testing is performed on the tooling after installing it at the customer plant. The results of the process validation testing of the tooling at the customer plant are used to adjust the occurrence ratings for the MFMEA and the PFMEA on the tooling after the installation. After this step, there is one MFMEA and one PFMEA. The MFMEA identifies the risk of the tooling installed in the customer plant not functioning as intended due to improper design. The PFMEA identifies the risk of the tooling installed in the customer plant not functioning as intended due to improper use.
5. Information gained from performing the MFMEA and PFMEAs is used to improve the tooling hardware and/or software, tooling use instructions, and tooling maintenance instructions before the tooling is allowed to move to the next stage.
Like the common RFMEA process described in Item 7, an effective tooling QMS includes a PFMEA on the tooling after it is installed at the customer’s plant. However, because of all the other risk-management tools used by the tooling QMS prior to tooling delivery and installation, it’s extremely rare to find new failure modes, new failure causes, or problematic prevention and detection controls with this PFMEA. Except for rare cases, the tooling problems detected by the PFMEA on the tooling installed at the customer plant are the result of variations in consumed materials that are difficult to duplicate on tooling built and installed at the tooling-provider’s plant.
9. The Ford RFMEA definition and how it differs from the most common RFMEA definition
Ford Motor Co., which is the only one of the Big Three to have an IATF 16949—“Customer-specific requirement” that requires using a RFMEA, provides the following RFMEA guidance:
“Organizations are required to have a process in place that ensures all new launches complete an RFMEA event once the equipment is installed and running. This process should be first completed at the equipment manufacturer and then after final installation on the organization’s plant floor. The reverse FMEA involves design and process engineers working with operators and attempting to make bad parts, beat the error proofing and find new failure-modes causes, and develop controls. The goal is to discover opportunities and implement improvements in the FMEA that were not previously discovered. Evidence of Reverse FMEA events must be available starting July 1, 2022, for forward model programs which have not yet completed Job 1.”
There is one key difference between the common definition of RFMEA currently being provided by RFMEA training providers and the Ford definition of an RFMEA: The Ford definition requires an evaluation of the tooling installed at the tooling provider before tooling shipment, and not just after installation in the customer plant. This aligns with the definition of an effective tooling QMS by allowing early detection of tooling issues.
10. What you should do to meet the new RFMEA usage requirement
Ford’s objective in requiring companies to use the RFMEA is to ensure that their suppliers effectively manage tooling risk. An effective tooling QMS will always include performing a PFMEA on the tooling after the build at the tooling-provider plant as well as after installing the tooling at the customer plant. The PFMEA will be conducted by tooling design engineers and the tooling customer personnel responsible for the use and maintenance of the tooling. The tooling QMS will also include performing process-validation testing at these two times. This aligns with the Ford CSR definition of what an RFMEA is.
Unlike Ford, many companies limit the definition of the RFMEA to the PFMEA and process validation performed after tooling installation at the customer plant because of the publicly available information on what an RFMEA is, along with currently available RFMEA training. Consequently, when presenting evidence of an RFMEA, companies that have an effective tooling QMS should identify the PFMEA and process-validation testing that’s performed on the tooling after installation at the customer plant as their RFMEA. The PFMEA and process validation on the tooling after installation at the tooling provider exist and can be shown if the auditor requests it.
If a company doesn’t have an effective risk-based tooling QMS in place, it should implement the activities found in an effective tooling QMS identified in Section 8 above, and provide the PFMEAs and process-validation results for the tooling both after installation at the tooling provider plant and after installation of the tooling at the customer plant as evidence to meet Ford’s RFMEA requirements. They will not only meet Ford’s RFMEA document requirements but also experience a considerable improvement in tooling quality and performance.