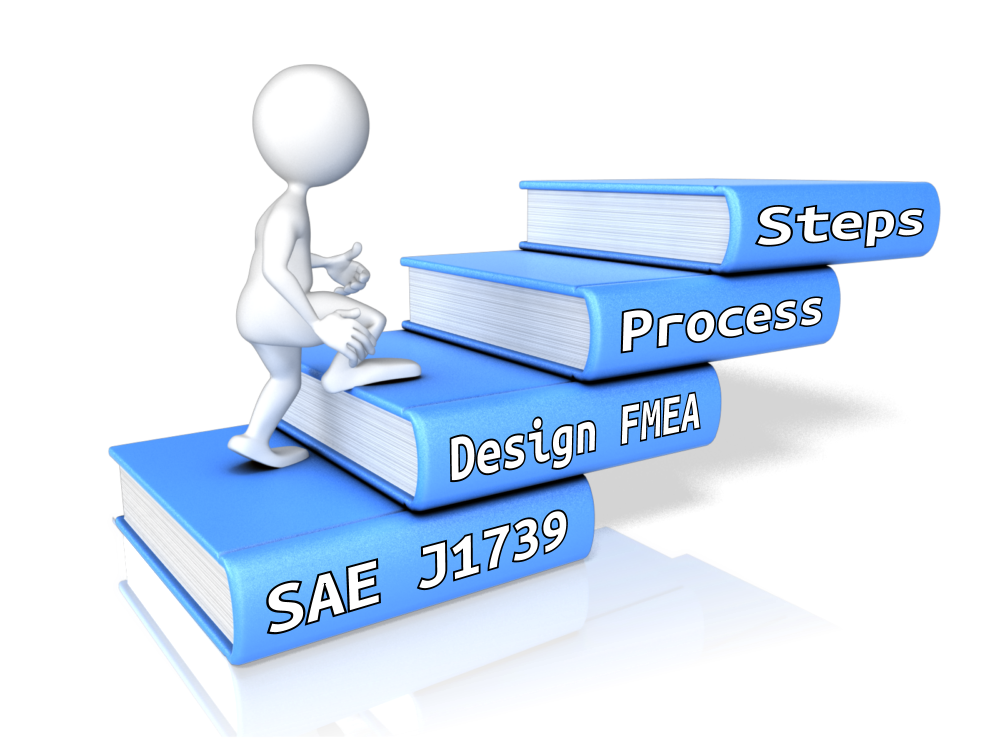
SAE J1739 FMEA Standard JAN2021 Series: Six Step DFMEA Process Overview
Introduction
The objective of this article is to provide an overview of the new SAE J1739 FMEA Standard six step DFMEA (“J1739 DFMEA”) process. Included is a general description of the contents of each of the six steps. Due to the numerous questions that I have been asked on how the six step J1739 DFMEA process compares with the seven step AIAG VDA FMEA Handbook DFMEA process, a reference on where to find the comparable information in the AIAG VDA FMEA Handbook is provided. Detailed analyses of the efficiency and effectiveness of the individual J1739 DFMEA process steps in implementing DFMEAs will be covered in future articles.
J1739 DFMEA Process Step 1: Project Planning
The first step of the J1739 DFMEA process titled “Project Planning” step covers the selection of the Design FMEAs for the project. The step begins with the identification of potential System (aka Assembly), Subsystem (aka Subassembly) and Component DFMEAs that may need to be performed. Elements that are critical to the selection of the potential DFMEAs to be created are the physical construction of the product and the reason for performing the DFMEAs.
Once the potential DFMEA candidates are identified, a methodology is provided to assign a preliminary risk rating to each of the potential DFMEAs. The risk rating is used to both determine which DFMEAs are to be performed and the sequence they are to be performed in. Once the DFMEAs are selected and the sequence of their performance determined, the information is documented in a project plan. The project plan identifies the DFMEAs to be performed, their sequence and the details of their implementation.
AIAG VDA FMEA Handbook Coverage Location of J1739 DFMEA Process Step 1 Topics
- AIAG VDA FMEA Handbook “2.1 DFMEA 1st Step: Planning and Preparation”
- AIAG VDA FMEA Handbook “2.2 DFMEA 2nd Step: Structure Analysis”
J1739 DFMEA Process Step 2: DFMEA Preparation
The second step titled “DFMEA Preparation” is performed for each DFMEA selected during Step 1. Step 2 covers multiple tasks. The first task is to develop the scope of the DFMEA to be performed. For example, if the DFMEA is to be performed on a Subsystem, the scope would define the subsystem components and interfaces that are to be included in the Subsystem DFMEA. The J1739 DFMEA process requires that a Block Diagram be used to assist in the performance of this task.
The DFMEA team is created during the second step as well as information collected for the performance of the DFMEA. Ground rules are provided for the information collection and its cataloging for retrieval. Included in the information could be a baseline DFMEA if one exists.
Step 2 also covers the identification and prioritization of potential Functions and Requirements for the DFMEA. A rating system is provided to define a “Function Priority” for each of the individual functions identified. An “Item/Function Matrix” is provided to capture the Items/Interfaces, Functions, Requirements and Function Priority information.
AIAG VDA FMEA Handbook Coverage Location of J1739 DFMEA Process Step 2 Topics
- AIAG VDA FMEA Handbook “1.5.3 FMEA Team”
- AIAG VDA FMEA Handbook “2.1 DFMEA 1st Step: Planning and Preparation”
- AIAG VDA FMEA Handbook “2.2 DFMEA 2nd Step: Structure Analysis”
- AIAG VDA FMEA Handbook “2.3 Design FMEA 3rd Step: Function Analysis”
J1739 DFMEA Process Step 3: Technical Risk Analysis
The first task accomplished during Step 3 is to use the “Item/Function Matrix” to populate the DFMEA with selected Functions and Requirements based on Function Priority. The J1739 DFMEA Standard also suggests the possible use of the “P Diagram” to assist in defining Functions for the DFMEA.
Once the “Function” column is completed, the “Potential Failure Mode”, “Potential Failure Effects”, “Potential Failure Causes”, “Current Prevention Control” and “Current Detection Control” columns are filled out.
AIAG VDA FMEA Handbook Coverage Location of J1739 DFMEA Process Step 3 Topics
- AIAG VDA FMEA Handbook “2.3 Design FMEA 3rd Step: Function Analysis”
- AIAG VDA FMEA Handbook “2.4 Design FMEA 4th Step: Failure Analysis”
- AIAG VDA FMEA Handbook “2.5.2 Design Controls”
- AIAG VDA FMEA Handbook “2.5.3 Current Prevention Controls (PC)”
- AIAG VDA FMEA Handbook “2.5.4 Current Detection Controls (DC)”
J1739 DFMEA Process Step 4: Risk Assessment and Prioritization
During Step 4, ratings are defined for Severity, Occurrence and Detection. These ratings are used to define the risk of each line of the DFMEA. The J1739 DFMEA Process identifies four forms of risk assessment: RPN, SxO, Criticality Analysis (aka Risk Matrix) and the AIAG VDA FMEA Manual Action Priority Rating (AP). Despite offering four different types of risk assessment, the J1739 DFMEA form only provides an entry area for the AP.
Special Product Characteristics are also defined during Step 4. The J1739 DFMEA process defines Special Product Characteristics as characteristics that could significantly influence product safety, performance, fit, and service life if they were incorrectly specified or the product was not built to the characteristic specification.
Step 4 also introduces the use of the FMEA-MSR. The FMEA-MSR, which is used in conjunction with the DFMEA, is a method for analyzing the effectives of fault handling features in the design in detecting the presence of Failure Mode Causes and/or Failure Modes and mitigating the effects of the Failure Modes. Step 4 provides instructions for the implementation of the FMEA-MSR.
AIAG VDA FMEA Handbook Coverage of J1739 DFMEA Process Step 4 Content
- AIAG VDA FMEA Handbook “2.5.7 Severity (S)”
- AIAG VDA FMEA Handbook “2.5.8 Occurrence (S)”
- AIAG VDA FMEA Handbook “2.5.9 Detection (S)”
- AIAG VDA FMEA Handbook “2.5.10 Action Priority (AP)”
- AIAG VDA FMEA Handbook “4 Supplemental FMEA for Monitoring and System Response (FMEA-MSR)”
J1739 DFMEA Process Step 5: Reduce and Communicate Risks
Step 5 covers:
- whether or not recommended actions are needed based on the risk of the row
- monitoring status of recommended actions for each row of the DFMEA when needed
- defining responsibility for the implementation of the recommended actions
- tracking results of the recommended actions
- actions to be taken if recommended actions do not provide desired result
AIAG VDA FMEA Handbook Coverage of J1739 DFMEA Process Step 5 Content
- AIAG VDA FMEA Handbook “2.6 Design FMEA 6th Step: Optimization”
J1739 DFMEA Process Step 6: Document Results
Step 6 covers the documentation of the DFMEA results and management and control of the DFMEA documentation.
AIAG VDA FMEA Handbook Coverage of J1739 DFMEA Process Step 6 Content
- AIAG VDA FMEA Handbook “2.7 Design FMEA 7th Step: Results Documentation”
Summary
Although the new SAE J1739 DFMEA six step process has one fewer step than the AIAG VDA FMEA Handbook DFMEA process and includes the FMEA-MSR in the DFMEA process rather than providing a separate section, there are considerable similarities between the two DFMEA processes. This is to be expected given the number of members who were on both the AIAG VDA and SAE J1739 FMEA committees.
In the next article, we will begin to analyze the J1739 DFMEA six step process for its ability to efficiently implement DFMEAs that can be used to effectively manage design risk. The first two elements of the J1739 DFMEA process analyzed will be how the process determines what DFMEAs must be done and how the the Function and Requirements columns of the J1739 DFMEA are populated.