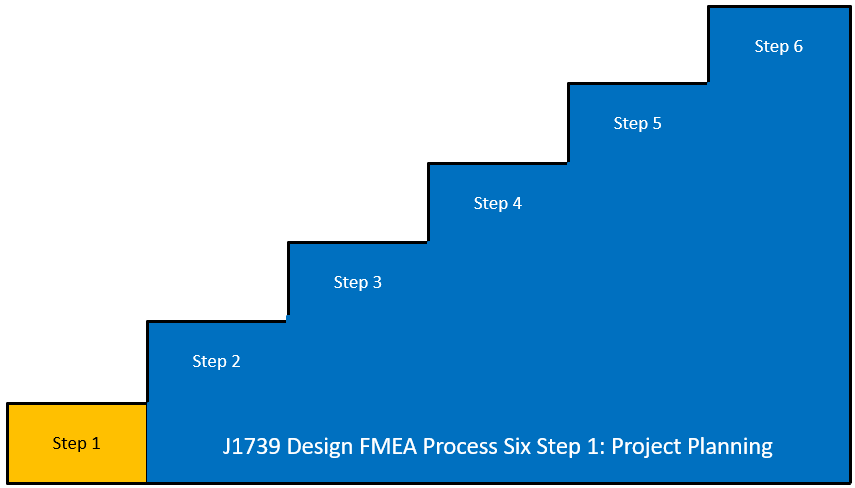
SAE J1739 FMEA Standard JAN2021 Series: DFMEA Process Step One
Introduction
Titled “Project Planning”, the first step of the new SAE J1739 FMEA Standard JAN2021 has six core elements. The six core elements are:
- Determine the “System Elements” (System, Subsystems and Components) that make up the product.
- Create methodology to perform Preliminary Risk Assessment of System Elements.
- Apply Preliminary Risk Assessment methodology to the System Elements to give each System Element a risk rating.
- Use the individual System Element Preliminary Risk Assessment results determine which System Elements need an individual Design FMEA to be performed on them.
- For the System Elements selected for performance of a Design FMEA, use the risk rating assigned to each System Element during the Preliminary Risk Assessment to determine their performance timing.
- Develop a documented Design FMEA implementation plan.
Step One Element One: Determine System Elements
The first step of the J1739 Design FMEA process and the creation Structure Tree created during the AIAG VDA Design FMEA creation process are similar. In fact, Section 5.1.1 of the J1739 standard references the AIAG VDA Structure Tree as a means of accomplishing this step.
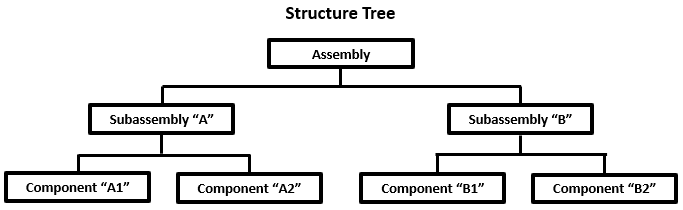
The first step of the J1739 Design FMEA process and the creation Structure Tree created during the AIAG VDA Design FMEA creation process are similar. In fact, Section 5.1.1 of the J1739 standard references the AIAG VDA Structure Tree as a means of accomplishing this step.
Step One Element Two: Create Preliminary Risk Assessment Methodology
Due to the resources required in the performance of a Design FMEA, the new J1739 standard provides methods for limiting the number of Design FMEAs to be performed.
The new J1739 standard first defines three reasons companies are exposed to risk and the performance of one or more Design FMEAs is required. The first is a new design or new technology. Under this condition, the new J1739 standard suggests that the Design FMEA process should be considered for the System as well as all Subassembly(s) and Component(s). The second reason for performing Design FMEAs is modifications to an existing design. Under this condition the new J1739 standard suggests that the Design FMEA process should be focused on the design changes. The third reason for performing Design FMEAs is that an existing design exists that will be used under different conditions than the original design such as changes in the environment of use or application. Under this condition, the Design FMEA process is to concentrate of potential risks due to usage changes.
The new J1739 standard suggests that the number of required Design FMEAs can further be reduced by performing a Preliminary Risk Assessment of the perceived risks at the System, Subsystem and Component levels. Although the standard is not prescriptive of the contents of the Preliminary Risk Assessment, it does offer an example. The example includes the following elements:
- Risk factors to be evaluated (i.e. Regulatory, Safety, Degree of Change);
- Assignment of a grade (1 = Low Risk, 2 = Medium Risk, 3 = High Risk) for each;
- Calculation of risk factor for each System Element by multiplying ratings;
- Define “Minimum Risk Rating for Performance of Design FMEA”.
Step One Element Three: Apply Preliminary Risk Assessment Methodology
The Preliminary Risk Assessment is performed on all the System Elements.
Step One Element Four: Select Design FMEAs Using Preliminary Risk Assessment Results
Any System Element that receives a risk rating greater than or equal than the “Minimum Risk Rating for Performance of Design FMEA” level should have a Design FMEA performed on it.
Step One Element Five: Schedule Design FMEAs Using Preliminary Risk Assessment Results
The scheduling of Design FMEAs for the selected System Elements should be based on risk ratings with the highest risk ratings performed first.
Step One Element Six: Create Documented Design FMEA Implementation Plan
Create a Design FMEA implementation document detailing the Design FMEA implementation schedule.
Problems with the New J1739 Standard Design FMEA Selection Process
In a previous article in the SAE J1739 FMEA Standard JAN2021 Series titled “What Is A Design FMEA?” we learned the following about the purpose of the Design FMEA:
“The Design FMEA is a risk assessment of the adequacy of the hardware specifications and/or software code in defining a product that will meet the design requirements. It assumes that manufacturing will build the product to the specifications.”
Like the AIAG VDA FMEA Handbook Design FMEA method, the new SAE J1739 standard Design FMEA methodology advises the designer to perform individual Design FMEAs on a Subassembly and Component basis rather than a single Design FMEA for all selected Subassemblies and Components that the design engineer is responsible for. The reason for the AIAG VDA FMEA Handbook Design FMEA methodology requiring the performance of Design FMEAs on a Subassembly and Component basis is that the VDA FMEA Software originally released in 1992 that is driving the AIAG VDA FMEA Handbook requires Design FMEAs to be done on a Subassembly and Component basis. In future articles, proof will be provided that the performance of Design FMEAs on an individual Subassembly and Component basis results in a Design FMEA process that is both inefficient and ineffective at meeting the Design FMEAs intended purpose.