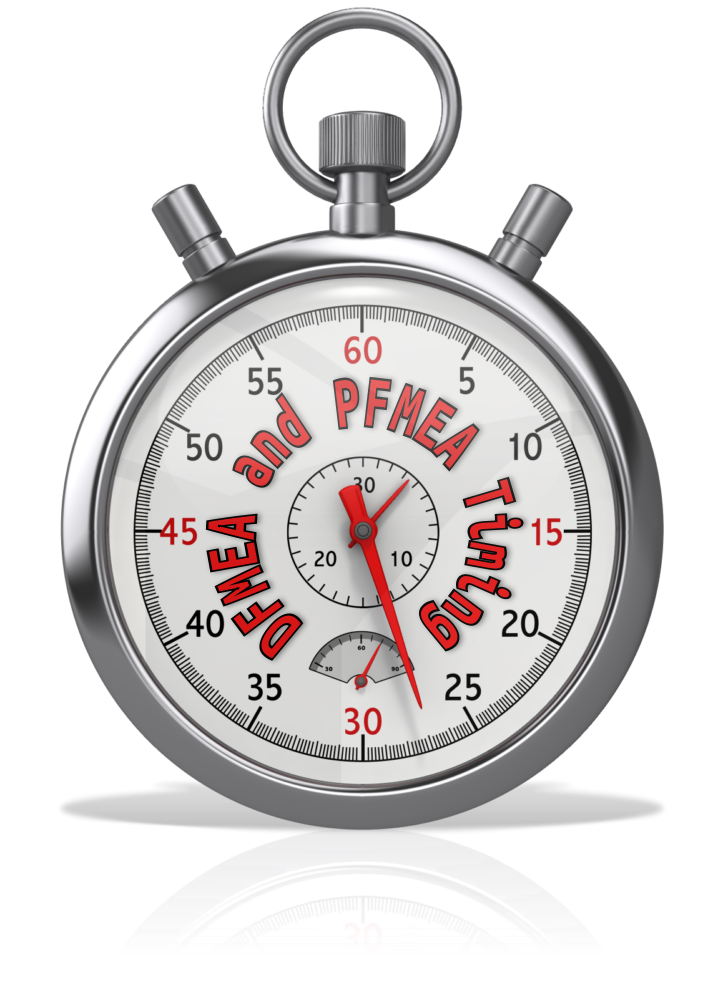
SAE J1739 FMEA Standard JAN2021 Series: Design FMEA and Process FMEA Timing
After 34 years of helping companies properly implement DFMEAs and PFMEAs to improve their product designs and manufacturing processes, I have seen a lot of mistakes in their use. Improper start and completion timing for both the DFMEA and PFMEA are common. If you attempt to perform the DFMEAs and PFMEAs too early, the participants find that they do not have the necessary information about the product and processes to properly populate the DFMEA and PFMEA forms. If you complete the DFMEA too late, the current design residual risk determined by the DFMEA is not available to determine if the product design should be released for manufacture. Similarly, if you complete the PFMEA too late, the current manufacturing residual risk determined by the FMEA is not available to determine if machine qualification should be started.
Objectives of Article
This article has two objectives. The first objective is to define what the new SAE J1739 FMEA Standard JAN2021 (Copyright © 2021 SAE International) says about the proper start and completion timing for the DFMEA and PFMEA. The second objective is to assess if the SAE J1739 FMEA Standard start and completion timing instructions for the DFMEA and PFMEA are correct.
What the SAE J1739 FMEA Standard Says the Design FMEA and Process FMEA Start and Completion Timing
The new SAE J1739 FMEA Standard states the following about start and completion timing for the DFMEA and PFMEA:
4.4.1 Start
“The FMEA should be started as soon as the design or process concept has been established.”
4.4.2 Completion
“The FMEA should be completed through action plan identification before the design or process has been finalized. In general, a DFMEA should be finished before validation testing begins. A process FMEA should be finished before machine qualification begins.”
SAE J1739 FMEA Standard Design FMEA Start Timing Instruction – Is It Correct?
Before one can define the proper start and completion timing for the DFMEA, one must begin by defining what a DFMEA is. The DFMEA is a structured risk assessment of the adequacy of the current hardware specifications and/or software code in defining a product that will meet the current product design requirements. Consequently, to perform a DFMEA one must have verifiable Design Requirements and defined hardware specifications and/or software code.
The SAE J1739 FMEA Standard states that the DFMEA should be started as soon as the design concept has been established. At this point in the product development process, it is rare that verifiable design requirements, hardware specifications and/or software code all exist. Consequently, it is not possible to perform a DFMEA on a design concept.
However, it is possible to perform a Fault Tree analysis on a design concept since only a general idea of the functions and potential failures of the assembly, subassemblies, components and interfaces that make up the product design must be known. Like the AIAG VDA Design FMEA methodology, the SAE J1739 FMEA Standard DFMEA methodology is based on the false premise that the base structure of the DFMEA and a Fault Tree performed on a design have equivalent core structures when they do not.
In conclusion, you cannot perform a risk assessment of the adequacy of hardware specifications and/or software code in meeting verifiable Design Requirements that have not been defined. One can begin to perform a partial Design FMEA on any verifiable design requirement of the product if the hardware specifications and/or software code that control if the product will meet the design requirement have been defined.
SAE J1739 FMEA Standard Design FMEA Completion Timing Instruction – Is It Correct?
The SAE J1739 FMEA Standard states that “a DFMEA should be finished before validation testing begins”. The definition section of the SAE J1739 FMEA Standard does not differentiate between design validation (analysis and/or testing to determine if the customer requirements are met) and design verification ((analysis and/or testing to determine if the design requirements are met) The following definition is given for Design Verification/Design Validation in the SAE J1739 Standard:
3.5 DESIGN VERIFICATION/VALIDATION: Analysis or testing executed to demonstrate that new or modified designs, or new applications of existing designs, will meet customer expectations, in the intended environment, over the useful life of the product.
One must assume the creators of the standard are using the terms validation and verification interchangeably and that the entries of the Design Prevention Control and Detection Control columns fall under the category of “validation testing”. When the DFMEA is performed correctly, the function of the Design Prevention and Detection Controls in the DFMEA is to define the Occurrence ratings for the Design FMEA. Consequently, it is impossible to meet the SAE J1739 Standard requirement that “a DFMEA should be finished before validation testing begins”. In a future article we will review the SAE J1739 FMEA Standard instructions provided for the completion of the DFMEA Occurrence Rating column.
The Design FMEA is never completed and should be maintained until the product design has been retired. Using the Design FMEA and the supporting Design Verification Plan as design risk assessment tools, the design must be shown to have an acceptable level of residual risk before the design is released for manufacturing.
SAE J1739 FMEA Standard Process FMEA Start Timing Instruction – Is It Correct?
Before one can define the proper start and completion timing for the PFMEA, one must begin by defining what a PFMEA is. The PFMEA is a structured risk assessment of the use of a previously designed process in producing a product which will meet product design hardware and software specifications. For new products, the PFMEA is often confused with the Machinery FMEA which is the equivalent of a DFMEA on the new process equipment required to build the new product. The Machinery FMEA is performed to assess the risk exposure due to the process equipment having inadequate capability to produce a product that will meet the product hardware specifications due to improper design. The PFMEA is performed to assess the risk of the new process equipment that has been proven to have the capability of producing within specification product being used incorrectly.
Given this definition, it is impossible to perform a Process FMEA on a “process concept” as the SAE J1739 FMEA Standard suggests. When the process equipment is in the “concept” phase one is trying to develop a set of process equipment design requirements that will be provided to the Machine Tool provider to design and manufacture the required equipment. In the concept phase, the details of the process equipment design are not available to perform a thorough usage analysis required by the PFMEA.
SAE J1739 FMEA Standard Process FMEA Completion Timing Instruction – Is It Correct?
As the SAE J1739 FMEA Standard suggests, “the process FMEA should be finished before machine qualification begins”.
Conclusion
You have learned that you can attempt to perform Design and Process FMEAs both too early and too late. Proper timing is essential if use of the DFMEA and PFMEA is to be both effective and efficient.